IPC J-STD-001 Standard – Soldering Requirements for Electrical and Electronics Assemblies
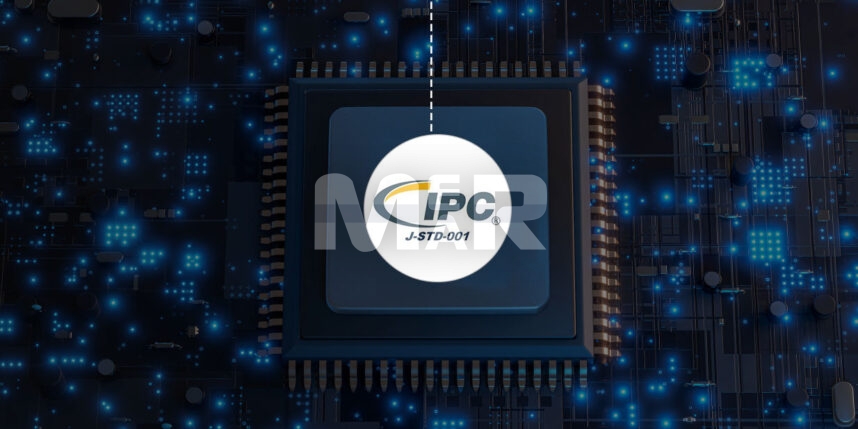
J-STD-001 has emerged as an important IPC standard for soldered electrical as well as electronic assemblies. The standard lays down the following:
- Material Specifications
- Process Requirements
- Acceptability criteria
Adhering to J-STD-001 standards essentially ensures that the soldering is of high quality & that it works well under different environmental conditions.
The standard was first released in 1992. Then known as J-STD-001 A, it has undergone several amendments with the latest version being J-STD-001H. Under the certification the following elements are included:
- Material & components
- Soldering requirements
- Terminal & wire connection
- Through-hole mounting
- Surface mounting
- Cleaning
- Coating & adhesives
Difference between J-STD-001 & IPC-A-610
The similarity between J-STD-001 & IPC-A-610 is that both delineate the soldering process & the characteristics of an acceptable board. However there are several differences between the two standards, namely:
- IPC-A-610 is an acceptable standard for electronic assembly acceptance
- IPC-A-610 also lays down the board inspection procedures
- J-STD-001 on the other hand deals with the material & processes for soldering in particular.
Let us look at some of the requirements as laid down by J-STD-001
Soldering Requirement as Per J-std-001
- It lays due emphasis on cleanliness as contamination of material as well as surfaces can lead to errors & malfunctioning
- It also lays emphasis on the heating & cooling rates. The use of chip capacitors ensures that there is due protection
- It is imperative that strands of wires aren’t damaged.
- Prior to the application of conformal coating a through soldering inspection needs to be undertaken
- Any soldering errors need to be reworked
- The use of Automated Optical Inspection & that of Automated X-Ray inspection is imperative
Industry Standard for Space Applications
In addition to this J-STD-001ES standard has been issued that applies to space addendum application. Some of the areas covered under that include:
1. Flux
Flux is categorized into RO & RE resin, which in turn has activity levels from L0 to L1. It is important to test the compatibility of the flux as well as undertake solder paste testing.
2. Material
In terms of material, it is important to validate as well as document any changes in flux, solder paste, cleaning media etc. Also, it is important to use solder alloys that are known for performance & reliability
YOU MAY ALSO LIKE: Right Material For PCB
3. Corrosion Plan
It is imperative to have a red plague corrosion control plan for silver-coated copper conductors
4. Chemical Strippers
The choice of chemical strippers needs to be done in a manner that it does not cause any damage. Also, it is important to protect components from thermal shocks. For this, the use of a heat sink, thermal shunt or more is recommended.
5. Mounting components
In terms of mounting of components, a suitable method needs to be followed so that the necessary temperature can be attained. Additionally there needs to be adequate clearance between parts. It is also important to offer stress relief to leads as well as to wires that attach terminals.
6. Exposed material
While exposed material is acceptable, the exceptions to this rule are components made of iron, component leads, Kovar & Alloy 42. Also, the exposed material should not hamper the process of forming the solder connection. Similarly, the OSP should not hamper the solder joint
7. Wire & Lead Ends
In terms of wire & lead ends, they should not extend over the terminal by more than one lead diameter. Also the electrical clearance requirements must be met.
8. Through-hole component soldering
In terms of through-hole component soldering, it is important that the PTH is completely filled with the solder.
YOU MAY ALSO LIKE: Through Hole Importance In PCB
9. Lead Length
There needs to be a minimum lead length. While for flat and coined leads it is two lead width, for round leads it is two lead diameters
10. Chip Components
In terms of chip components, there are separate requirements for rectangular or square chip length components as well as for cylindrical ones.
11. Surface Mount Area Array packages
The visual inspection requirements for array packages include an X-Ray or AOI inspection. The visual inspection must also cover the solder termination. In case of corner markers on the board, the area array components need to align in X & Y directions. There shouldn’t be errors in terms of absence of leads.
12. Ultrasonic Cleaning
Ultrasonic Cleaning is recommended when there are only terminals or connectors present on bare boards or where it is documented that the use of ultrasonics will not impact the performance of the assembly.
It is imperative that the J STD 001 training be attended by anyone who is in charge of soldering electrical or electronic assemblies such as assembly operators, quality inspectors, manufacturing engineers & more.