Understanding Complete PCB Assembly Cost & Factors that Impact the Cost
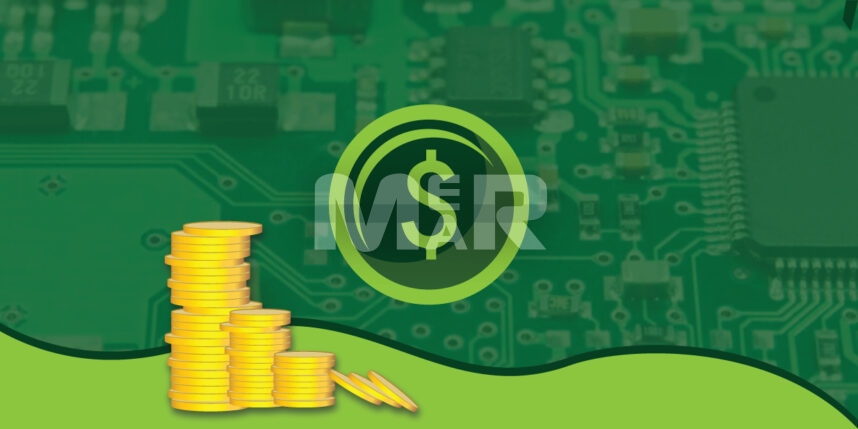
In the PCB industry, balancing manufacturing costs and product quality is a huge challenge. You need to identify the expenses involved in each stage of PCB development. There are multiple factors affecting the quality of PCB during fabrication and assembly. Knowing the PCB assembly cost breakdown can assist the designer in choosing the right components for the PCB design. Along with the pricing of the components, features like the board size, PCB material, number of layers, type of PCB assembly method, etc impact the overall PCB fabrication and assembly cost. Further services like testing, packaging, and shipment will add to the total PCB production cost. Collaborating with an experienced contract manufacturer (CM) will benefit in reducing costs and building quality PCB products.
There are some assembly challenges commonly observed during PCB manufacturing. They can be a shortage of components, non-standard PCB dimensions, wrong positioning of the inspection equipment in the assembly line, and many more. In turnkey PCB assembly, your CM will have an excellent network for component sourcing. This helps procure genuine parts at lower prices. It is recommended to add alternate parts to the Bill of Materials (BoM), especially for components that are specific to your board functionality. Choosing a standard PCB size may not be viable in many cases. But both large and small boards can add extra assembly costs. After PCB assembly, it is crucial to inspect the board for any visible placement and soldering faults. Your CM should have the latest assembly setup with optical inspection machines suitably placed in the assembly line. This is essential to increase line efficiency.
PCB Assembly Cost Breakdown
If we break down the various components of a PCB assembly cost, it will be mainly the following four items:
1. Bare board cost
Usually, PCB fabrication and assembly are done together. The cost of bare board manufacturing depends on the material selected, the number of layers, and the board size. You must share the Gerber file and other important PCB design files with your CM for the PCB fabrication.
2. BoM cost
This is the expensive part of a PCB assembly. The bill of materials provides the list of all components and sub-assemblies required for the product assembly. You may have to keep margins for material wastage during the PCB assembly.
3. PCB Assembly cost
The type of assembly technique used determines the labor and engineering requirements of the PCB assembly. Mounting the components on the bare board is a critical process. Surface Mount Technology (SMT) method is commonly used and is cost-effective.
4. Board Testing cost
The assembled PCB must undergo visual inspection and functionality testing. It is recommended to include PCB testing and debug support from your CM. This will save time and assist your CM in improving the assembly line for the next production batches.
It is beneficial to know the various aspects that influence PCB assembly pricing. This will guide you in optimizing the overall PCB production cost.
Factors affecting the PCB assembly cost
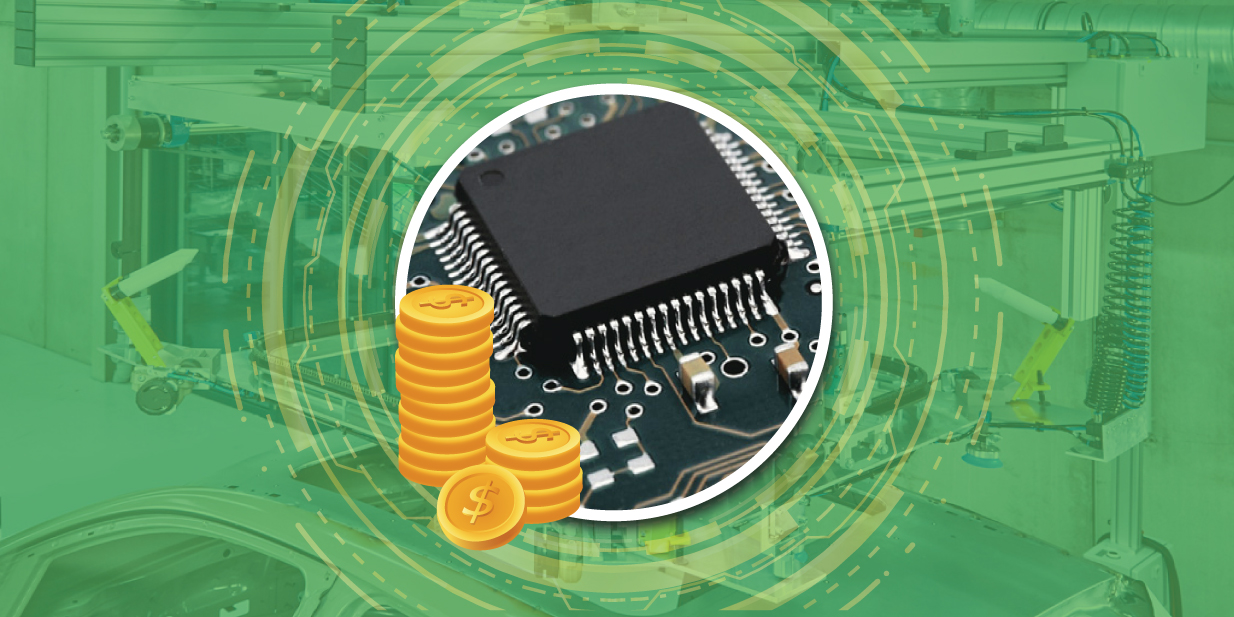
1. PCB dimension and thickness
The assembly cost increases with the board thickness. Drilling holes in bulky boards is complex and involve precise apparatus. Non-standard PCB sizes will require customized assembly panels, adding to the expenses.
2. Lead time
Some CMs can deliver PCB assemblies in just one working day based on the volume and design complexity. But it will be very expensive. You can opt for a longer lead time and reduce the assembly cost with prior planning.
3. Build volume
It is recommended to estimate the product requirement for over a year and then place the assembly service order. High build volumes will be cheaper as the setup charges and one-time expenses will be covered altogether. Many CMs provide good discounts on bulk orders.
YOU MAY ALSO LIKE: Ways to get low-cost PCB assembly
4. PCB Design complexity and customization
Increased board complexity calls for higher assembly charges as it affects the engineering and labor costs. If you require customized PCB assembly like ruggedized PCBs for harsh environments, then the price shoots up.
5. Chosen PCB assembly method
All the latest PCB assemblies are built using the SMT method. But some special circuitries require a Through Hole Technology (THT) approach. This is expensive and suitable for small build volumes. Surface mount parts are best suited for compact PCB designs. If your circuit board is designed using SMT components, then the assembly cost will be drastically reduced.
6. Board and component materials
Choosing the board material is mainly dependent on the circuit functionality. FR4 is the commonly used substrate and is cheaper compared to polyimide material. Electrical components are available in several packages. Leadless packages like BGA or QFNs are expensive. Discrete parts purchased in reels are economical. Your CM can guide you in picking cost-effective components for your PCB design.
7. Coating and Surface finish
To make a PCB corrosion-resistant and durable, surface finishes and coatings are essential. The PCB assembly cost varies with these add-on services. Based on the application, PCBs may require complete or partial surface coatings. The number of coats, coverage tolerances, etc affect the pricing accordingly.
8. PCB Assembly standards and compliance
CMs put in long-term investments to comply with the industry standards like ISO 9001, ISO 13485, and AS9100. Also, assembling RoHS (lead-free) compliant PCBs require a special manufacturing setup. These factors will add to the overall PCB assembly costs.
9. Assembly Technology
Broadly surface mount technology costs lower than through-hole technology. Additionally, some PCBs may also require using ball grid arrays or BGA assembly which impacts the assembly costs.
10. Test and Packaging requirements
Based on the level of testing required for your assembled PCB, the cost will vary. Choosing basic tests like visual inspection and power-on tests may be cheap. But if you require JTAG or functional testing then the cost will increase. Product packaging price increases for EMI sensitive PCBs.
11. Shipment and Delivery
The quick-turn PCB shipments are costly. The delivery schedule directly affects the assembly charges. The labor wages depend on the quantity and schedule of shipment orders.
Conclusion
The above-listed factors can guide you in optimizing your PCB assembly pricing. Your focus should be on the quality of PCB along with cost reduction. An experienced CM can support you in assembling high-performance PCB at a minimum cost.
Opting for Mermar Electronics is the most prudent decision if you desire to avert probable complications, simplify the procedure, and economize on both time and cost. We provide an all-inclusive range of PCB services that entail PCB assembly, fabrication, and design, all under a single roof. To request a quote, kindly fill out the form below, or send an email to sales@mermarinc.com .