How to make low-cost PCB prototypes for your next project?
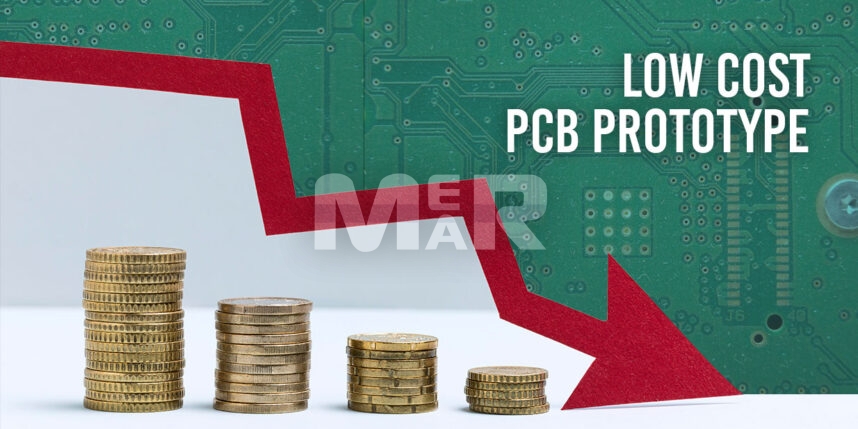
Before we look at some tips that help you to make low-cost PCBs prototypes, it will be worthwhile to look at what a PCB prototype is and why it is used in the first place.
What is a PCB prototype & why is it used?
Essentially a PCB prototype is an early sample of the final board. It is required to help test the basic functionality of the PCB board design. PCB prototypes can be of various kinds, such as:
- Visual Models
- Working Prototypes
- Proof-of-concept
- Functional Prototypes
While a visual model will give a fair idea of the physical aspect of the product, a functional prototype will be close to the final product.
Importantly, a prototype helps with finding out any design flaws at the early stage itself. This results in saving you costly errors at a later stage. The prototype helps test a modern design quickly before you get to the mass production stage.
What does PCB prototype cost include?
The cost of a PCB prototype comprises of the following elements:
- Material
- Board Size
- Speed
- Complexity
In addition, factors that increase the cost of PCB Prototype include:
- Incomplete documentation.
- Components may not be available or may be End of Life. This will involve researching for alternate components.
- The design itself may not be production ready.
- Prototypes involve several Design for Assembly, Design for Test & Design for Debugging Components.
- Time to market is typically short & that requires the contract manufacturer to fast track operations and have dedicated team members available.
- Quantity has a major impact on costs.
How to achieve low-cost PCB prototype
By being mindful of the following aspects you can reduce the cost of the PCB prototype:
1. Design Optimization
It is important to optimize the design in a manner that makes fabrication easier. Using fewer and cost-effective parts is yet another way of lowering the cost of the PCB.
2. Panelized Prototype
Higher number of PCBs on the same panel, go a long way in optimizing costs.
3. Component Procurement
Ensure that component procurement is done with a view to optimize costs. Ensure, for example that the component procurement time is reduced and the purchase team is well equipped to look for alternatives with lower costs. Pro tip- Do not overlook the fact that some supplier will offer you good rates for a big MOQ order, which you cannot afford at the prototype stage.
4. Choose your contract manufacturer with care
Last but not least, it is imperative that you choose your contract manufacturer with care. You must look for a PCB contract manufacturer that offers low cost without compromising on the quality.
It is also imperative that you involve them at the PCB design stage itself. With access to industry best practices they will be well placed to figure out any flaws in design early & save you from costly errors. Some of the aspects to look for in choosing the right contract manufacturer include:
- Are they equipped to offer prototype services as not all companies are?
- Do they have design expertise, and can they help you with the development of PCB design?
- What kind of experience do they have & what is their portfolio like?
- Can they offer you quality assurance?
- Do they provide you with a full documentation package?
- Do they have a vast network of vendors?
- How flexible are they to respond to requests for changes?
- It will be an innovative idea to read client reviews or even to seek out their customers.
To sum up
The importance of a PCB prototype cannot be overstated. They can go a long way in reducing the total costs of the project as also its timeline. They are a wonderful way to test your design early as also to test components individually & collectively. They can be used to spot any potential issues early & make the necessary changes. With the right best practices & involvement of professional contract manufacturers you can ensure that the price of the prototype is optimized.
We are a California-based PCB manufacturing company, who provides services from prototyping to manufacturing. We follow the industry’s best practices and ensure standard-quality PCB prototypes.
email us at sales@mermarinc.com or call us at (760) 244-6149 for a quick quote and other details.