What is PCB BOM management? How to streamline production with It?
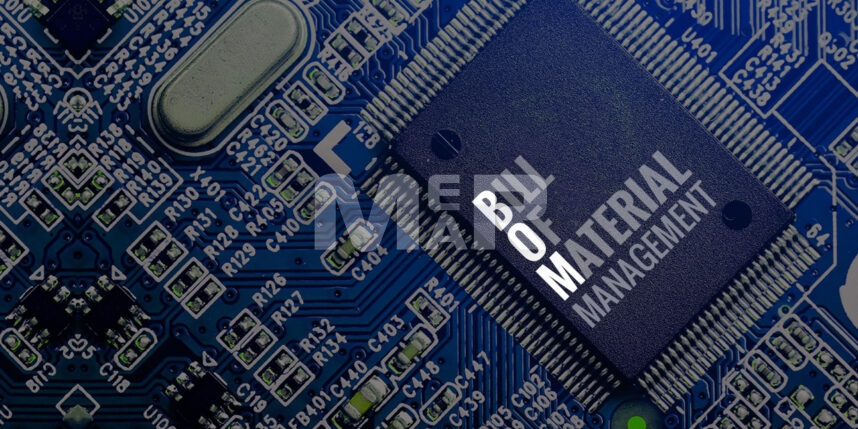
The beginning of the PCB manufacturing process involves listing down the parts, sub parts assemblies & more that will be required in production. In other words, creating a Bill of Materials or BOM, as it is commonly known as.
A Bill of Material is essentially a detailed list of all parts that are used in production. The manufacturer needs to refer to the BOM at various stages to ensure that all inventory is in place and the production is seamless. Proper PCB BOM management plays an important role in:
- Management of Inventory
- Product Lifecycle Management
- Quality Control, and more.
Use of BOM in manufacturing
For a robust BOM to be built, it requires input from various departments. While the engineering team can offer specifications of the product, the purchase teams facilitate optimal costs. The marketing team uses it to ensure that the functionality is communicated to the customer.
Typical information in a BOM includes:
- Part Number
- Part Name
- Quantity
- Description
- Procurement Phase, and more.
YOU MAY ALSO LIKE: How to create PCB BOM (Bill of Materials)?
BOMs, in turn, can be single-level or multi-level. The key difference between the two is that a multi-level BOM also lists the child parts that are needed to make the parent parts, which in turn, go into the assembly of the final product.
Need for PCB BOM management & ways to streamline production with it!
With several departments requiring access to BOM, the old paper documents or even spreadsheets aren’t adequate. Also, paper documents lend themselves to manual errors. Besides in case different departments need to make revisions there is always the fear of duplication not to mention the fact that tracking of different versions is a huge challenge.
PCB BOM Management to Streamline Process
What comes in handy therefore are cloud based BOM solutions. BOM Management goes a long way in streamlining production. Here is how:
1. Centralized BOM Management System Control
Different departments require access to the BOM. It is important therefore to centralize the management system control. If this is done, you can create a central repository. Importantly it makes easier to collaborate across departments. Any changes that are made therefore do not cause any confusion & versions are easy to track.
2. Secure Access
Often, besides your internal team, you may also need to offer access to BOM to suppliers. BOM Management allows you to offer secure access. Additionally, you are also able to offer access to any changed suppliers or any other additional parties. All this significantly reduces time lags & ensures a seamless production.
3. Accountability
With a BOM Management solution you can also identify the revisions & edits & the people responsible for them. This ensures that accountability is maintained.
4. Proactive Assessments on BOM Components
These days it is imperative to source products that are environmentally compliant. It is therefore equally important to provide this compliance information to the right people in the supply chain. This ensures that quality is maintained, delays avoided and costs kept under check. With BOM Management it is easy to streamline this process.
5. Improves Collaboration
What the BOM Management process also allows you to do is to leverage informal communication methods. With the ability to provide inputs it enhances product development as it makes collaboration easy for the teams while enhancing traceability & team continuity.
6. Improves Product Lifecycle Management
BOM also aids in product lifecycle management in the following ways:
- It becomes a single repository for all information.
- It records all changes & revisions & lends itself to traceability.
- Offers ease of assessment of cost.
- Ensures seamless data handover.
- It connects the design as well as purchase processes.
7. Accelerates Product Launches
When it comes to new product launches, speed is of the essence. In effect what a robust BOM enables you to do is to eliminate any manufacturing or PCB fabrication errors that stem from use of wrong parts, as well as stem any quality issues. With mechanical, software & electrical designs coming together for all product teams, new product development is significantly enhanced. In fact, engineering change review timelines can be severely cut. With collaboration improved between supply chain partners, errors are also significantly reduced.
It also ensures that disconnected silos do not exist as also brings about real collaboration between distributed teams. All this together results in quick time-to-market, a source of significant competitive advantage.
With automated BOM systems, you can, therefore, not just maintain optimal stocks, utilize real time data, integrate inputs from all departments, and more.
With the help of Mer-mar electronics, you can get quick time-to-market PCB assembly production and other competitive advantages you cannot get enough of. Submit your BOM file now to get a quick PCB quote.