The PCB Components Assembly Process – A Complete Guide!
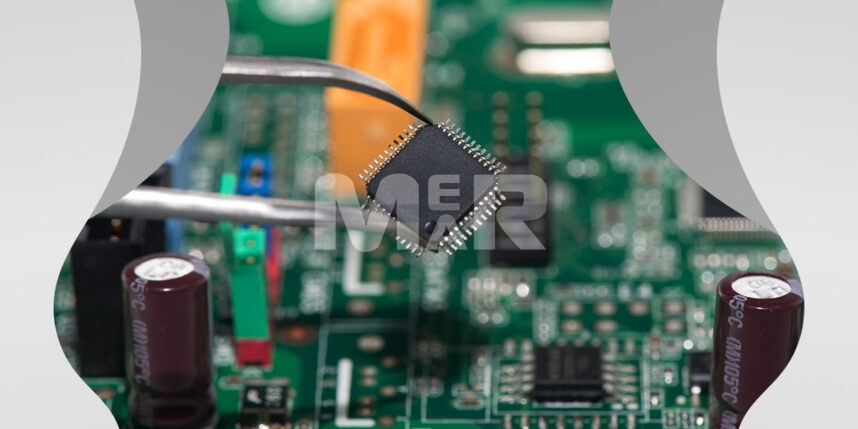
When it comes to the assembly process of PCB components, there are both automated as well as manual steps involved depending on the complexity of the board. Of course, the assembly process also has a lot to do with the fact whether the assembly is being done for through-hole components, surface mount components or whether they are mixed PCB components.
THROUGH-HOLE PCB COMPONENTS
Typically, these are components with long leads and are a generation behind surface mount components. These components involve that leads be inserted into holes and then soldering them. Typically such components are only mounted on the top end of the board.
PCB DESIGN
While designing PCBs with through-hole components, it is important to place the holes at distances that are specified by the component manufacturer. When dealing with multi layered printed circuit boards What is also important are plated through-holes. These holes also act as vias for connecting circuits on the outer layers.
For such boards since drilling of holes is a key requirement, the area that is available for routing of traces is limited. That typically means that you have to use a board with a large area that may not be conducive to the trend of miniaturization that is prevalent. Alternately, you can use a board with multiple layers.
COMPONENT MOUNTING
Whether you choose to use manual or automated component mounting, it is important that the component leads are pre-processed so that insertion becomes seamless.
SOLDERING
Largely, through hole components are soldered by a process of wave soldering. The machine throws up molten solder through a nozzle. As the components assembly passes over this wave, the components are soldered in place.
SURFACE MOUNT PCB COMPONENTS
For such components, the exercise of drilling need not be undertaken. In fact these are smaller components that can be packed together and they work particularly well in dense assemblies. Also surface mount components can be mounted on both sides of the board.
PCB DESIGN
Since space does not need to be allocated for the holes, a high component density is a given. High density is also achieved by using small vias or tented vias in pads when it comes to fine pitch components such as BGAs (Ball Grid Array packages).
SOLDER PASTE DEPOSITION
The use of a stencil to deposit solder pads at the right areas is important. Solder paste deposition may be manual or automated.
COMPONENT MOUNTING
Typically pick-and-place machines are used to mount small components. This ensures that each component is mounted in the right location with solder paste on the pads.
SOLDERING
Since solder paste is already present all that is required is to melt the solder so that the component is held in place. For this purpose, a reflow soldering machine comes in handy. It has infrared heaters that generate heat that melts the solder paste & fixes the components.
MIXED PCB COMPONENTS
Some applications make use of a mixed technology & hence use both surface mount as well as through-hole components.
PCB DESIGN
In such cases the surface mount components are typically placed on the underside of the board. This is advantageous as the wave soldering process ensures that they are soldered along with the through-hole components.
COMPONENT MOUNTING
For the surface mount components it is important to use a glue deposition process. Essentially a dispenser places glue between the pads. The pick-and-place machine next mounts the surface mount components. Pro tip – It is important for the board to go through a curing process so that the glues is sufficiently hardened & the component is held in place.
SOLDERING
It is now safe to turn over the board & insert the through-hole components. After this follows the wave soldering process.
To sum up
While PCB assembly of through-hole components seems simpler, the fact remains that there could be opportunities for failure. For example, if component leads are close there are chances of shorts. Also, a big disadvantage with through-hole components is that they do not lend themselves to high density assembly.
Surface mount components on the other hand can take care of many of these issues. The components can be packed densely. Also, with the reflow soldering process the quality of soldering is far higher.
Mer-Mar Electronics is one of the leading PCB manufacturing companies, providing all-in-one PCB assembly solutions. Our consistent quality & quick turnaround endear itself to our customers, who look on us as a one-stop shop for all PCB manufacturing requirements.
If you have any queries regarding our surface mount assembly or through-hole PCB assembly services, or need urgent assistance, then please do not hesitate to contact our team of skilled personnel. Send us an email with your queries at sales@mermarinc.com or call us at (760) 244-6149.