Tips to Overcome the Factors That Slow Down PCB Manufacturing
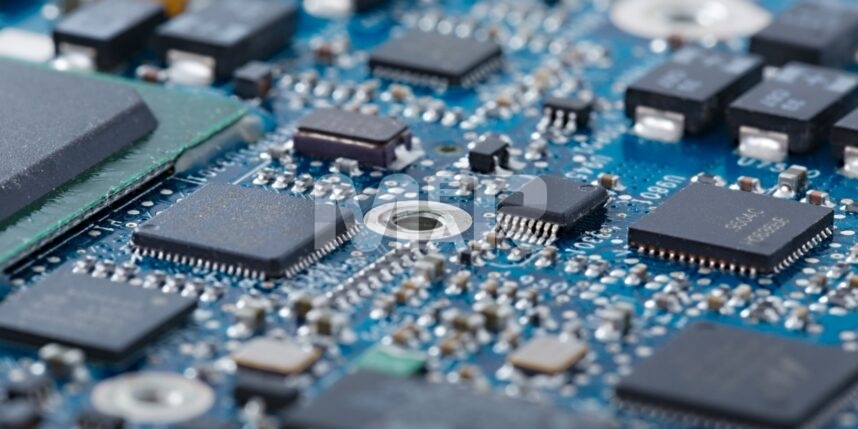
Printed Circuit Boards are becoming ubiquitous in today’s environment where we tend to use enough and more electrical devices in many aspects of our lives. Circuit boards containing the complex circuit array that they do, both their design and quality is of tremendous essence when it comes to the efficiency of the final product.
Complexity of printed circuit boards also increases their chances of failure on account of factors such as oversights in design, errors in drilling, over etching and more. In today’s highly competitive market where go to market time is of essence in the success of your product, you certainly cannot afford to lose time. Each error and potential failure of the PCB can in turn cause costly delays. What you need, therefore, the right PCB partner who can offer you quick turnaround times without compromising on quality.
Factors That Slow Down PCB Production
A close look at some of the common factors that can slow down the PCB manufacturing process is imperative so that you can keep these factors in mind in choosing the right partner. Here is a handy checklist that you can refer to while making your choice:
1. Delays in Prototypes
If you are setting out on a new business or expanding your product line, the one thing that you need for sure is a prototype. For the same you need to work with a company that has a quick turnaround time when it comes to developing prototypes. Not only do you need a manufacturer that can provide you these prototypes without delay, you also need someone reliable who can understand your requirements and deliver a prototype that is as per your requirements. Delay in receiving the prototype or receiving a prototype that does not meet your requirements can equally lead to a whole lot of delays down the line that slow down the manufacturing process.
It is imperative therefore that you choose a PCB partner who has a proven track record when it comes to both delivery time as well as understanding your exact prototype requirement. Only with such a partner can you be sure that the prototype will work the way it should and therefore your timelines will not be jeopardized.
YOU MAY ALSO LIKE: PCB Manufacturing Tolerances
2. Creating PCB boards yourself
Given the fact that you could experience delays in receiving prototypes from some PCB partners, you may often be tempted to create PCB boards yourself if you have some amount of technical knowledge. This approach, can lead to a host of costly mistakes besides consuming a lot of your time, which could otherwise be used in other productive aspects of business. The net result could therefore still be delayed time to market. Spending some time to research a partner who is extremely professional and can deliver PCB boards on time and with accuracy is therefore a productive means of avoiding delays.
A professional partner will take a number of factors into account at the design stage itself. These include proper placement of products which if not done correctly can among other things lead to overheating. In fact, the risk of creating PCB boards yourself, is often burned components. Also, with a quality partner, you can rest assured that the components that are used are of high quality and that traces and pathways are in order. There are a whole lot of issues that need to be kept in mind such as proper PCB soldering process, sufficient board thickness, and more which the PCB partner on account of his vast experience will be privy to, but which you may not be exposed to and therefore could easily miss.
3. Setting unrealistic expectations
Another aspect that is known to slow down PCB manufacturing sometimes lies not so much with the PCB partner but in the fact that one tends to set expectations that aren’t realistic. These expectations may be by way of cost of the product or turnaround times. It is imperative that you undertake through research so that you set expectations that are not out of sync with reality. This will in turn help you in creating a product roadmap that will be sustainable.
On the other hand, on occasions you could also come across PCB partners who might offer you turnaround times that seem extremely appealing but which are at the same time, unrealistic. With your research in place this should raise red flags as in case you go ahead with these unrealistic expectations you are likely to meet bottlenecks on the way that could derail your entire plan.
If there is one common learning thread running through the checklist, it is the fact that enough time and energy should be spent on doing thorough research on doing thorough research on the credentials of the PCB partner so that you can consciously avoid these bottlenecks.
Want to Get Your PCB Assembled from Mer-Mar Electronics? Send us inquiry to Get a Quick Quote based on your custom requirements.