All About Aluminum PCB: Types, Process, and Applications
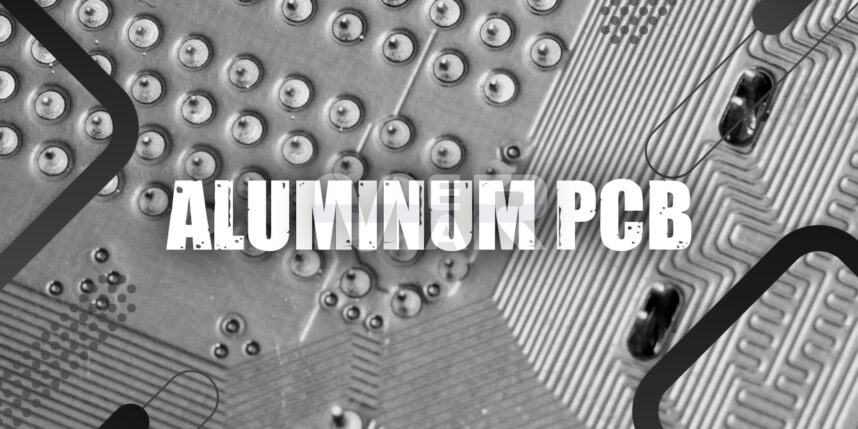
Metal Core Printed Circuit Boards are known to find use in several applications. Aluminum PCBs are one of these which are quite popular. Such PCBs are known for their electrical insulation & thermal conducting capabilities. When it comes to applications with high power & tight tolerances, their importance cannot be overstated.
Composition of an Aluminum PCB
Aluminum PCBs comprise of the following layers:
1. Copper Foil Layer
It is a thick layer of copper which is responsible for the higher current carrying capacity of Aluminum PCBs. The copper foil ranges from 1 to 10 ounces.
2. Dielectric Layer or the Insulating Layer
A thermally conductive layer, it is known for its insulation, bonding as well as dissipation of heat.
3. Aluminum Base
Made of aluminum substrate it is known for high thermal conductivity.
4. Aluminum Base Membrane Layer
It keeps the surface protected from scraping & etching. Typically, this layer has a thickness of 1 mm.
Process of manufacturing Aluminum PCBs
The various steps involved in manufacturing of aluminum PCBs include:
- Pretreating Aluminum PCB laminates
- Generating circuits on the copper layers
- Drilling holes on production panels
- Solder mask printing
- Silkscreen printing
- Choosing the surface finish
- Punching & routing the PCBs
YOU MAY ALSO LIKE: Silkscreen VS Solder Mask
Types of Aluminum PCBs
Broadly there are multiple types of aluminum PCBs, the choice of which depends upon the application in which they are being used. These include:
1. Through-hole Aluminum PCBs
Largely in such PCBs the aluminum is pre-drilled and laminate material applied.
2. Flexible Aluminum PCBs
As their name suggests they offer a high level of flexibility on account of the flexible dielectrics that are used. With such flexible PCBs, the need to use connectors is highly reduced.
3. Hybrid Aluminum PCBs
These find wide use in RF applications. They use a non-thermal material as the sub-assembly, which is bonded to the Aluminum base using thermal materials.
4. Multi layered aluminum PCBs
These have multiple layers of thermally conductive dielectrics. They are extremely suitable for heat conductivity in complex products.
What makes Aluminum PCBs so popular in various applications?
On account of its wide range of advantages, Aluminum PCBs find use in several applications. Some of these include:
- They are light in weight and hence work very well for miniaturized, light-weight applications. Despite their light weight they are known for their strength.
- They are known for their heat dissipation quality. With aluminum PCBs, you can rest assured that on account of its superior thermal expansion performance, the various components on the board have improved shelf life. Once again in case of high temperatures, aluminum substrate retains dimensional stability.
-
Aluminum PCBs come with a number of environmental benefits as they are non-toxic and also recyclable.
YOU MAY ALSO LIKE: Reasons to reuse or recycle PCBs
- With widespread availability of aluminum, these PCBs are economical & therefore do not increase the cost of the PCBs.
Where do Aluminum PCBs find use?
Aluminum PCBs are particularly preferred in applications that require effective heat dissipation. Some of the applications where there is widespread use of Aluminum PCBs include:
- Audio Equipment
- Power supply equipment
- High power LED Lights
- Automotive applications
- Office automation equipment
- Power modules
- Industrial power equipment
- Interior lighting
- High-power scanners
- Solar cell substrates
- Semi-conductor refrigeration devices, and more.
To Sum Up
Aluminum PCBs are game changers because they offer improved heat dissipation, and they are extremely cost-effective. It is important to use the right contract manufacturer who has the requisite experience in manufacturing Aluminum PCBs.
In the absence of rich experience, the PCB manufacturer may face issues related to areas such as solder mask printing where a thick copper foil can hinder solder mask printing.
For this, using a quality solder mask oil or filling in resin before the solder mask are an effective solution.
Similarly, it is important to know how to store aluminum PCBs as they attract moisture. When you partner with Mer-mar Electronics you can rest assured that you will get the right product. Mer-mar Electronics is ISO-9001:2015 AS9100D Certified who has 40 years of experience in PCB assembly and PCB fabrication. Fill out the form below to request a free quote now.