SMT Line Guide: Overview, Process, and Equipment Used!
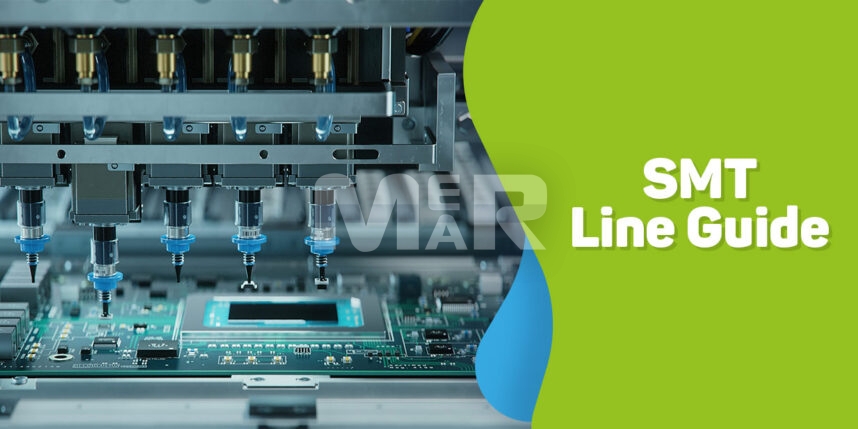
SMT Line or Surface Mount Technology Production Lines imply the manufacturing facilities that enable PCB assembly and their subsequent testing. The SMT production process can in turn be broken down into smaller processes, each of which requires different machines, all of which, in turn, comprise the SMT Line.
Types of SMT Lines
In turn, SMT Production lines can be of two kinds:
1. Automatic SMT Line
Essentially where the pick and place machine are fully automatic.
2. Semi-Automatic SMT Line
Where there is the need to manually load/unload PCB boards.
SMT Line Process
The broad process in assembly involves:
- Applying solder paste to the PCB
- Placing components
- Using the reflow process to solder the boards
- Testing
Let us look at each of these processes in some detail:
1. Applying Soldering Paste
This involves printing the paste on the board with the help of a silk screen. A custom stencil ensures that the solder paste is applied only in the requisite areas. Once it is ascertained that the paste is evenly applied, it is time for component placement and assembly.
2. Component Placement and Assembly
In this process, the electronic components are loaded. The assembly machine then removes each component, and places it in the exact position on the board where it needs to be affixed. The next process involves the boards to be put in a reflow oven for soldering.
3. Component Soldering
The reflow soldering process involves the boards being warmed with heated air. In turn, this results in the melting of the soldering paste. This ensures that the components are fused to the PCB. The boards are subsequently cooled ensuring that the components are well fused to the board.
4. Testing
It is important that a thorough inspection be undertaken to ensure that the quality of the boards is robust. For this Automated Optical Inspection is made use of. Through this method, the system automatically checks each board, and any deviations are highlighted. Not only does this ensure accuracy, but it also makes sure that costly mistakes are avoided later.
Equipment used in SMT Lines
Below is an overview of the main equipment that is used for SMT lines.
1. Pick and Place Machine
This is the most important equipment for SMT lines. As its name suggests, this machine picks up the surface mount components & places them accurately on the PCB pads.
2. Solder Paste Mixer
This equipment is responsible for accurately mixing the solder powder & paste. It goes a long way in standardizing the operation & besides of course saving labor.
3. Oven
An oven is required to bake PCB boards & to remove any moisture from them.
YOU MAY ALSO LIKE: Eco-friendly PCB and DFM Best Practices
4. SMT Loader
It is responsible for placing the PCBs into the solder printing machine.
5. Solder Paste Printing Machine
As its name suggests, it is used to print solder paste on to the boards.
6. Solder Paste Inspection Machine
This is instrumental in checking that the solder paste is printed properly on the PCB.
7. Reflow Machine
Reflow soldering ensures that the solder melts & the components therefore fuse with the board. Reflows can be of several types, the main ones being:
- Hot Air Reflow
- Infrared Reflow
- Hot gas Reflow, and more.
8. AOI (Automated Optical Inspection)
This performs a crucial role in checking for any placement failures both pre- and post-solder. With any errors highlighted at this stage, it saves a lot of time, effort and money that could be otherwise spent correcting any errors.
9. Docking Station
Simply put, this is a connection station for the different equipment that make up a SMT line.
10. SMT Unloader
After reflow soldering an unloader both receives and stores the final circuit boards.
Needless to mention that the automation of the above processes goes a long way in:
- Standardizing the process and ensuring that each board adheres to the exact specifications.
- Weeding out any errors, timely.
- Resulting in savings in terms of labor costs and effort.
The role of automation particularly cannot be over-emphasized when it comes to PCBs that are used in mission-critical operations where the smallest of errors can have fatal consequences.
To avoid such errors and to make error-free PCB end products contact Mermar Electronics. We are an ISO 9001:2015 certified PCB assembly manufacturer who provides custom PCB fabrication. Contact us at sales@mermarinc.com or fill out the form below to request a free quote.